A&M – Modern Methods Boost Belgian Linen Biz
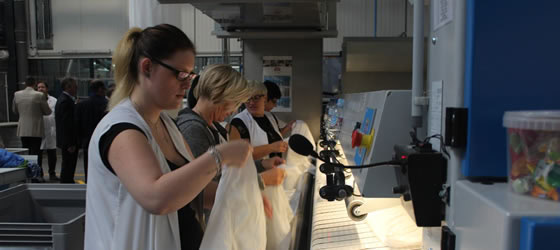
When you step inside the Ardennes & Meuse (A&M) laundry in Vottem, Belgium, you get a sense of the future of commercial laundering, worldwide.
The plant, located about an hour from Brussels, processes roughly 15-25 metric tons (33,000-55,000 lbs.) per day of hotel and food and beverage (F&B) linens in a highly automated washroom that uses the latest low-temperature wash chemistry to conserve energy and maximize efficiency.
“They are always interested in being the first in innovation,” said Eric Dethor of Chrysteyns Laundry Technology, who led about a dozen TRSA members and guests through the plant as part of last October’s tour of four Belgian laundries. TRSA organized the visits in advance of the World Textile Services Congress (WTSC) in Bruges, Belgium.
The A&M plant is 99% “steamless,” using a hot water heater, instead of a conventional boiler, which saves energy. It also makes extensive use of heat reclamation throughout the multi-level, 5,574 square-meter (60,000-square foot) plant. To get the work out with quality and precision, the plant has plenty of advanced machinery, including an extensive system of conveyors and overhead rails from JENSEN that helps reduce manual labor as much as possible.
FACILITY WALK-THROUGH
Our tour began at soil sort. This area includes a full JENSEN Futurail Continu-Sort fully automated sortation and monorail system. We moved quickly to the wash aisle, where we saw four Senking Universal P50 tunnel washers with Senking SEP50 Plus extraction presses from JENSEN. Three of the tunnels have 13, 50 kilo (110 lb.) chambers; a fourth has 14, 50 kilo chambers. All of these machines use Chrysteyns “Cool Chemistry” which enables them to wash between 50° and 60° C (120 and 140° F). When we asked why A&M doesn’t wash at even lower temperatures, Rudi Moors, president of Chrysteyns’ U.S. branch, explained that the reason is savings in the dryer. In essence, while the detergent would be effective at cleaning textiles at less than 50° C, a higher temperature enhances cleaning, while achieving the best possible balance of energy in the laundry and reducing drying times. “Keeping the temperature at a higher level allows for maximum cleaning as well as maximum efficiency in the dryers,” Moors said. The detergent features surfactants and enzymes in an environmentally friendly formula that meets all local wastewater-discharge requirements.
After washing in the tunnel, “cakes” of clean wet goods emerge from the press and move via conveyor to a bank of 12 JENSEN DT 120, 120 kilo (264 lb.) dryers. To enhance energy savings, these machines are equipped with Cyclone dryer heat-recovery equipment, which generates a 20% savings, Dethor says. In addition to water reuse in the tunnels, the plant has a rainwater-collection system that helps reduce its use of fresh water.
The pulsing rhythm of pop music from a boom box set the pace as we walked to the finishing area. Conveyors and a fully automated JENSEN Futurail clean-side monorail system move the bulk of the dry goods from the wash aisle to finishing for the next phase of production. Here, we see eight ironer lines; six are Lapauw machinery and two are JENSEN. Five are designed for large pieces, primarily sheets, with JENSEN large-piece spreader feeders. The other three are for smaller pieces such as pillowcases and napkins. Three of these ironers are fitted with spectrometers that measure the level of whiteness in various textiles to ensure customer satisfaction.
The plant also has 12 small-piece folders from JENSEN for bath linens and similar items. Among these are Butterfly Tematic Pros for folding towels and a Butterfly Maximat 900 Bathrobe, a specialized folder for terrycloth bathrobes used in high-end hotels.
As is common in European plants, but relatively rare in the United States, this plant has a JENSEN Jenrail, an overhead staging system for sheets that are automatically fed as needed into the ironers. Employees connect the sheets to two clips. Then the textiles whiz up to the ceiling like ghosts. Another sheet is clipped and—whoosh—up it goes.
On the back side of the ironers, an assortment of JENSEN automatic folding/stacking equipment prepares the textiles for the movement via JENSEN Jenway, an automated conveying system with traffic control and automatic sorting that leads to metal cages. Staff load these carts, and the drivers of the plant’s fleet of 15 trucks roll the cages onto vehicles for delivery to hotels and restaurants across Belgium. The plant operates with a staff of 40 people, and goods are tracked with JENSEN Cockpit, a plant-automation software package.
MARKET TRENDS
The linen supply market in Belgium—not unlike the United States—includes a wide range of independents, including large to midsize companies like A&M, as well as smaller firms that cater to small restaurants and “bed and breakfast”-style hotels, said Wim Demeyer, sales network manager for Lapauw. Demeyer accompanied TRSA members during the pre-WTSC tours. Larger companies tend to dominate the uniform side, but independents have a greater presence in other sectors. “You have the big groups that are specialized in workwear and are also in specialized in services like cleanroom,” said Demeyer, who’s based at the company headquarters in Heule, Belgium. “They tend to work in workwear and for these specialized services, while flatwork is going back to smaller laundries that can give them good quality and good customer service.”
A&M, a third-generation family-run business, is an example of an independent that’s competing successfully in the linen supply trade. Founded in 1950, Hubert Broers took over the La Meuse laundry later in that decade. His son Joseph began leading the business in the late 1960s, and his son Marc joined the firm in the 1980s. The company started out as a retail establishment for laundering the personal clothing of local residents, as well as processing professional wear.
In the 1990s, the laundry’s business mix shifted to hotels and food-service outlets, sometimes called “Horeca” (i.e., hotel-restaurant-café), according to the company’s website at www.a-mlocation.be. The professional and personal clothing sidelines were phased out in the early 2000s and in 2008, respectively, the site says.
Today, A&M specializes in rental textiles, although many hotel accounts are processed separately to ensure quality and consistency. Commercial Director Mark Broers’ main focus is on satisfying linen supply customers, while at the same time conserving resources. “To meet the needs of the Horeca sector,” the website notes, “We have chosen to offer a complete service, meeting the requirements of the sector, while respecting environmental standards.”
Based on everything we saw during our plant tour, A&M is meeting these twin goals of satisfying customers, while operating a sustainable laundry. And with the help of advanced automation, the company is achieving the efficiency and throughput necessary to secure its future in the linen supply market in Belgium.