EMI/PMI: Executives Gather In-Person for Industry Education
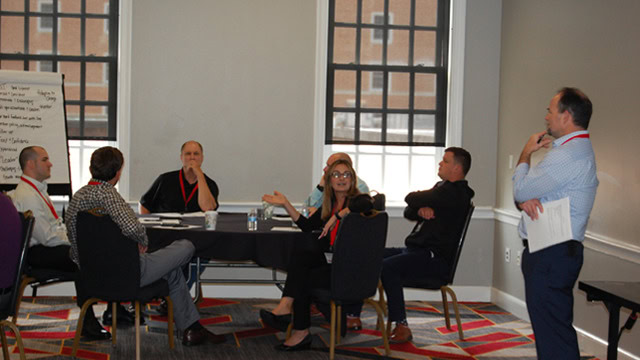
With more than 100 attendees taking classes and networking Aug. 8-12 at the University of Maryland, TRSA’s Executive Management Institute (EMI) took place for the 56th time and Professional Management Institute (PMI) for the 31st, reflecting participating companies’ and individuals’ firm commitment to in-person skill development through industrywide collaboration.
Their participation also spoke to their respect and admiration for each other, especially among the 10 graduates of EMI, who advanced through four annual iterations of the program this year to complete it; and four of their PMI contemporaries, who finished after two such sessions, testing at the program’s conclusion to earn the Certified Professional Laundry Manager (CPLM) certification.
COVID-19 did not deter third-year EMI student Greg Kimmel, service manager, Kimmel Corp., Upper Sandusky, OH, from returning. “I wanted to come back because the rest of the class did,” he said. It was rewarding to see them again and benefit from learning how their careers had proceeded. Even after two years of separation from the class (last year’s EMI and PMI were cancelled), classmates recognized each other’s career tracks and empathized accordingly.
Linen, uniform and facility services industry managers have had opportunities since COVID to learn from each other face-to-face through company meetings (multi-location operations) and cost groups of independent operators like the one in which Kimmel Corp. participates. The TRSA management institutes add an academic perspective to industry education, Greg noted, fostering skill development, which sets them apart from other industry groups and programs.
EMI’s group education setting refines participants’ skills by exposing them to emerging management techniques currently emphasized by academics and consultants and practiced by industry peers. When they return from EMI to their everyday roles, they’re better equipped to motivate and inspire co-workers and employees to streamline production, improve productivity and increase profitability.
The curriculum aids development of skills for more effective leadership, communication, innovation, change management and conflict reduction. Such enrichment enhances coaching, delegating, managing resources, problem-solving and team-building. Improvement follows in the attendee’s organization’s customer service, human resources management, workplace safety, legal compliance and other functions.
Until this year, the “P” in PMI stood for “production,” indicating that individuals directly responsible for managing laundry production personnel get the most from the program. This remains the case, but now the P means “professional,” as PMI’s more recent attendee lists show that managers and executives in almost all industry functions benefit greatly from this immersion in industry fundamentals by better recognizing how these affect their jobs. Attendees have included general managers and professionals in administration, business development, engineering, human resources, marketing, purchasing, sales, service and more.
Academic techniques used at PMI compel participants to rely on their experience and talent in contributing to class discussions. Group projects foster management creativity through envisioning everyday operations scenarios that require leadership or technical skills to address. These exercises test problem-solving, judgment and expertise. Dilemmas prompt participants to reveal and develop savvy in evaluating, comforting, coaching and disciplining workers.
Second-year PMI student Scott Voldbaek, regional sales manager, Pellerin Milnor Corp., Kenner, LA, praised the program for helping attendees develop a “broad spectrum” of skills, especially in the second year, when the curriculum turns to management techniques, shifting from focusing on laundry production strategies and tactics in the first year. He theorized this year’s classes were smaller than previously because of COVID-prompted labor shortages. “Managers can’t get away from their plants. They’re busy feeding ironers instead of managing production,” he observed.
For Voldbaek, returning to PMI as soon as possible to complete the program and earn the CPLM was in large part a matter of ensuring Milnor’s return on investment in enrolling him. “As soon as I received the email announcing the return of the program, I wanted to be there. If my company was going to make that investment in me, I was going to get it done as soon as I could.”
EMI student Kasey Wahl, marketing and sales director, Washing Systems (WSI), Cincinnati, pointed to the high level of interaction between classmates as a key draw. Of the third-year EMI program (in which he participated this year), he remarked, “there is no other situation where a group of people with as many different backgrounds can grow such a strong bond that will last forever.”
Regarding COVID’s impact on the program, he commented, “The gap provided everyone a little extra life experience to discuss and share with each other. Connecting again, even after an extra year, was great because you’re with a group you get to know just a bit more every year.”
EMI first-timer Brian Kimmel, business development director, Kimmel Corp., had a fair idea of what to expect, as his brother Greg had attended twice before. He looked forward to the presentation of “management concepts, theories, and thought processes that go into becoming a better leader” as opposed to the “concrete” concepts discussed in cost groups. The Year I classes reminded him of college but weren’t redundant because he took them in a different context: at the current stage of his career path.
The EMI experience enables participants to “take the time needed to understand your processes and where you’re going.” Performing daily routines can be like getting stuck in a gerbil wheel, he observed; to change that and improve results, personal strategies and tactics must change. EMI delivers a wealth of ideas to that end.