Operators Tour Two Top-Flight Vegas-Area Laundries
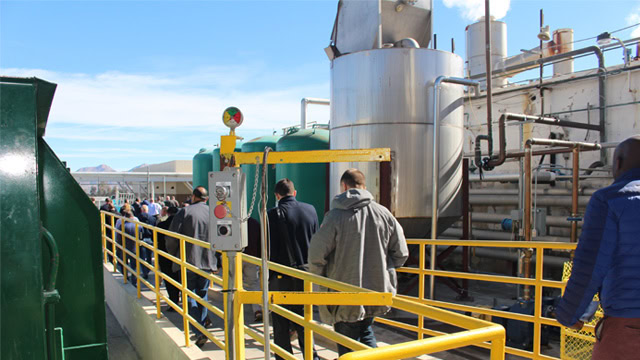
Roughly 100-plus attendees at TRSA’s recent Food and Beverage (F&B) and Hospitality Conferences in Las Vegas enjoyed visits to two leading area laundries catering to restaurants and hotels in and around “Sin City.”
The Feb. 5 tours were included in the back-to-back Hospitality and F&B Conferences staged at the Westin Las Vegas Hotel and Spa from Feb. 3-6. Each conference kicked off with a CEO roundtable that drew more than a dozen attendees. These sessions were followed by a full day of industry education, including presentations by top consultants to the hospitality and restaurant industries, plus facilitated attendee roundtables and panels comprised of customers, operators and vendors.
The tours kicked off with a visit to the 100,000-square-foot (9,290-square-meter) Boyd Gaming Linen and Uniform Service plant in Henderson, NV. Located roughly 20 miles from the Las Vegas Strip, this central laundry facility processes hotel, uniform and F&B textiles for 12 Boyd Gaming properties in metro Las Vegas, according to a handout provided to attendees.
Darryl Haase, director of linen & uniform services for Boyd Gaming, led our tour, which included a walk-through of this plant that processes 54,000-57,000 lbs. (24,453-25,854 kg.) per day. The mix of goods here is 86% hospitality linens, 10% F&B and 4% uniforms/specialty items. The laundry is unique in that it was the first in the United States to qualify as a Silver LEED-certified plant, reflecting its focus on environmental excellence. It’s also certified as a Nevada State OSHA Safety Health Awareness Recognition Program (SHARP) plant.
That’s welcome news to the plant’s roughly 95 employees, who work a single 10-hour shift in the plant that operates 365 days a year.
Moving to the wash aisle, we saw a White Conveyors Inc. overhead rail system and wash aisle machinery from G.A. Braun Inc. The latter includes two 16 module, 130 lb. (60 kg.) tunnel washers. These 12-year-old tunnels continue to run well, but if they or any other piece of wash aisle equipment requires outside help, Braun technicians are available, Haase says. “We get awesome service. I’m a Braun fan.”
He’s similarly pleased with the reverse osmosis system from U.S. Water that’s saved up to 20 million gallons to date. The plant’s water use averages 1.5-2 gallons per lb. processed.
Among the vendor representatives on-site for the tour was Michael Soussa, director of sales for Norchem Corp. He stood near the plant’s NORFLOW-WIN G4 chemical-injection system with cold-water chemistry. Soussa told us chemicals for the wash aisle are all piped in from a container-storage area, so there’s no need for “day tanks.” The reduced need to refill tanks makes spills less likely, he said. “They have great technology,” Haase added, speaking of Norchem. “The pipes are all stainless steel.” He estimates that the cold water wash is saving the company roughly 30% on natural gas with excellent wash quality. Sewer discharges are always in compliance with local rules. “Our water comes out cleaner than when it went in,” Haase says. “The city of Henderson (NV) should be grateful.”
Moving to the finishing aisle, we saw several ironer lines equipped with Chicago Dryer Co. equipment. “I love the Chicago products,” Haase says, pointing to a new spreader/feeder for sheets. Other equipment includes a Colmac tunnel finisher and a heat exchange system from Thermal Engineering of Arizona.
Visitors milled about the plant freely, then gathered near a front entrance wall that featured an elaborate company timeline with photos and graphics documenting Boyd Gaming’s history from 1975 to 2018.
Next, the attendees boarded two buses and headed for the Alsco Linen and Uniform Rental Services plant about 20 minutes away in North Las Vegas. General Manager Beau Murchison greeted the visitors and led one of several tour groups through the refurbished plant, parts of which date back to the 1940s.
As we entered the plant, we walked by an extensive rail-dock loading system for bags of soiled goods. Inside, the 88,000-square-foot (8,175-square-meter) plant features:
- 11 Ellis Corp. side load washer/extractors (eight 900 lb. [408 kg]; and three 445 lb. [201 kg.])
- Five CLM tumble dryers (1.1. BTU each)
- A Chicago Dryer Co. blanket blaster that takes large flatwork pieces and presents a neatly folded package when the goods leave the unit.
This tour included several presentations by vendors, including Steve Twombly, president of Automation Dynamics LLC. He described the company’s “Bullet” vacuum system that was installed in the plant to accelerate the movement of sorted goods to the washer/extractors for processing. Overall, the plant processes roughly 57,600 lbs. (26,126 kg) a day with a staff of 121 people. The plant also recently received TRSA’s Hygienically Clean Healthcare certification. While Alsco’s North Las Vegas plant processes primarily F&B textiles, healthcare comprises roughly 12%-15% of total throughput, Murchison said.
Other vendor representatives on-site included Spindle. Todd Leeth, Spindle’s strategic growth leader, described his company’s newly installed production-tracking system. Chicago Dryer, Tingue and WSI also had representatives available to answer questions about their products and services.
Snacks and drinks were provided at the end of the tour. Attendees lingered for nearly an hour, asking additional questions and networking with industry colleagues at the end of the program. They then boarded buses to head back to the hotel. Thus concluded TRSA’s Hospitality Conference, while the F&B Conference would have its kickoff at 3 p.m. that afternoon with TRSA’s Executive Roundtable for F&B executives.